Ordnance Survey has undergone its biggest behind-the-scenes change in data capture for a decade thanks to a new geospatial production platform. David Jones explains how it has made its operation faster, more agile and more evolutionary than ever before.
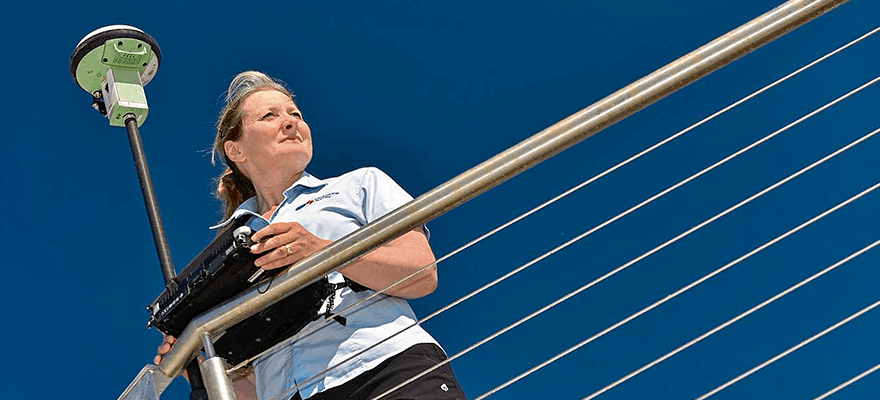
When Ordnance Survey (OS) won the contract from the Geospatial Commission in 2020 to provide the Public Sector Geospatial Agreement (PSGA), change was needed.
If it were to meet the demands of delivering the next generation of location data for Britain, with its richer datasets, improved currency, new ways to access OS data and freedoms for sharing data, its production platform had to improve.
The production system is at the core of OS’s business operations. It supports its external supply chain which captures 85 per cent of OS’s manual data updates, alongside surveyors and remote sensing teams, and will soon be rolled out among OS’s field survey team too. All users contribute to capturing and maintaining the core data asset that supports all of OS’s downstream products.
The old production platform (GDMS, the Geospatial Data Management System) was built 10 years ago and introduced to OS as a big bang implementation, where everything went live simultaneously.
This caused significant disruption to OS’s production levels and had a knock-on impact on customers that took some time to recover. This time around, a key objective for introducing a new system was minimal operational disruption to avoid impact to customers down the line.
Furthermore, the new platform was required to support ongoing and regular change to the data model and features within it, enabling OS to be more responsive to the needs of its customers.
The new geo-production programme is fundamentally re-platforming each part of OS’ core data capture and maintenance system. This includes the core database at the heart of OS’ products and services, the front-end data capture tools used by all production teams and the system that manages the interactions between the two. It also includes the provision of imagery to support data capture as well as automatic change detection. Working closely with Esri, OS is implementing a new technology stack, utilising commercially available off the shelf components (COTS) and configuring these to support ways of working across its various teams and data capture and maintenance flowlines.
OS Senior Project Manager Sasha Catchpole said: “In the past, OS has been unable to change at pace. For example, with the core products our customers use, there were long lead times for us to give notice and implement the changes.”
Re-platforming to GSPP
This inflexibility had to be tackled, and as part of the multi-year PSGA investment OS built itself a new system – the Geospatial Production Platform (GSPP). A next generation platform designed to be ever evolving and never sit still. Similar to most modern software providers, it enables OS to implement changes and enhancements and resolve system and data issues at pace – a step change compared to previously.
Sasha said: “Our customers want their data more quickly, they want it in a more configurable way, taking features and just the parts of products that they need.
“This new platform creates a lot of efficiencies for our internal teams. But the knock-on impact is that it’s quicker to deliver changes to meet our customer needs. If someone comes to us and says we want to see this new feature type, within your data, it is very quick for us to change the underlying data model, put those changes into the editing application and roll that out to our production teams to capture.”
Implementing GSPP is a mammoth task. Both the new and old system are running concurrently, to support OS’s transitioned teams and those still working under the old system. The first go live was delivered through a pandemic and with the challenges of remote working. In March last year, staff in the UK began work at 3.30am in the morning for weeks to train supply chain partners in India on the new platform. All 450 users from the supply chain were migrated within six months. Internal users at OS followed, with field surveying production teams set to begin the transition in June.
Despite this extra workload, there was no impact to OS’s data capture production output throughout that time.
Model office testing
To ensure the new platform provided effective and efficient capabilities, a Model Office approach was used to directly collaborate with data capture experts. This is where a production-like environment is used to access early releases of the system to test functionality and new business and operational processes. It helped OS developers to understand key processes and ensure the continued delivery of data to customers once the platform went live. It also enabled the development to be shaped by users and customers throughout the programme.
Senior Production Consultant Stacey Carrington said: “The Model Office approach has given us a significant win by encouraging collaboration between developers and end users. By getting the actual users working alongside testers you get more insightful feedback on the system and production processes.
As this development affects the day- to-day work of end users, it has been really significant that they can get their hands on deliverables as soon as possible, rather than wait for a big reveal at the end.
“As with the first phase of the roll- out (in which we worked iteratively with our supply chain to deliver and get feedback on updates), our surveyors are now able to test the platform in the field before implementation. Getting real ‘live’ feedback has been really positive.”
Benefits
The move to web-based applications also means OS is no longer restricted by its old centralised system. New layers, configurable apps and online tools can be utilised for more efficient production management and improved currency The system can be quickly adjusted, utilising the latest developments from across the industry. By being online, any update is automatically delivered to everyone, simplifying maintenance and reducing costs.
The previous platform required over 1.5 million lines of bespoke code. Under GSPP that has been reduced to just over 43,000 lines. This simplification has brought significant benefits to OS’s ability to maintain and change solutions and keep up with the latest versions of underlying technologies.
OS Director of Technology and Design Jo Shannon said: “One of the big drivers for this whole investment has been to give us more flexibility and freedom to change. One of the statistics I like most is that in the run- up to go live we changed the data model six times in the last three months. Compare that to only being able to make two or three changes to the data model in the last 10 years. That was because it was really hard, cost a lot of money and took a lot of time.
“Now we can respond to new customer requirements and market needs without it taking years or costing millions of pounds. That’s a win-win for OS and its customers.”
David Jones is Senior Press Officer at Ordnance Survey in Southampton, Hampshire (https://www.ordnancesurvey. co.uk/)