As the construction sector battles through turbulent times, Andy Flood explores how businesses can transform their workflows and improve profitability through digital upskilling
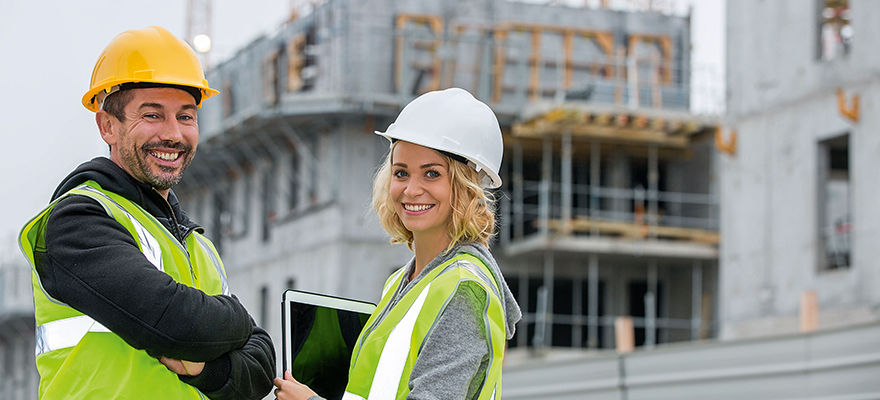
Over the last eighteen months, the construction industry has been confronted with a host of new issues such as material and labour shortages, price rises, and the increased National Insurance rate.
Nor do the pressures stop there. With more ambitious housing and net-zero government targets, contractors are finding it more difficult than ever to deliver projects on time, on budget, and to a high standard. The one solution that can help them improve their productivity and efficiency is the adoption of digital technology. However, to make this successful, contractors must address the need to upskill employees to make the most of digital solutions.
What caused the skills shortage?
The construction industry has struggled with a skills shortage for the last decade, which has significantly impacted the progress of huge projects like HS2. Negative attitudes towards digital and a preference for traditional methods has meant some companies have been stuck in the past rather than moving with the market. The result is increased labour costs, wasted resources, more errors, and delays where manual work is influenced by factors such as absences or poor weather.
While the last few years have seen an increased uptake of digital solutions, there are still many companies who are not making the most of their investments due to a lack of training. This has caused a further problem in that contractors who initially invest in digital solutions fail to use them correctly to realise their full ROI potential.
According to the latest CITB report on Building Skills for Net Zero1, the industry would need an additional 350,000 FTE workers to deliver the volume of work needed to reach Net Zero by 2050 using current construction methods. Contractors must start to consider how they can upskill their teams to use digital solutions to ensure they do not fall behind and lose out on the huge contracts that will be available as the government invests in new housing and net zero projects over the coming decades.
Was there progress during the pandemic?
Last year’s lockdowns meant that the construction industry had to find new ways to manage projects to deliver on time, accurately and to budget - all from remote locations as teams were told to stay away from sites. The only answer was turn to digital technology that allowed for fully remote project management. For example, the Sisk motorway bridge replacement project was managed remotely via Microsoft Teams and Bentley Systems Synchro, thereby allowing for a digital rehearsal of the build.2
Now that restrictions have eased, the industry is trying to recover and deliver a huge backlog of projects. To achieve this as quickly and accurately as possible, contractors are looking at how they can utilise digital within their workflows – but the one challenge that they are struggling to overcome is the widening skills gap.
While many contractors still view digital solutions as new and advanced technology, the software has been available from manufacturers such as Topcon for decades. It can seem daunting for construction workers to start using these digital tools if they have not received the correct training. In some cases, contractors have invested thousands of pounds in digital solutions and yet, being unsure as to how to make best use of them, have misjudged it a waste of money. To help overcome the fears and pitfalls of digital adoption, the government and manufacturers such as Topcon are offering free demos, training and after sales support on all purchases.
Emerging training needs
During the height of the pandemic, manufacturers and suppliers had to find new and remote ways of delivering product training and support. Online solutions such as myTopcon portal were upgraded to meet the needs of customers during that difficult period – including an enhanced remote support service.
This improved technology meant that the support team could recognise pilot errors more easily and educate users about why they were experiencing issues and how to prevent them, e.g., by using remote support via Topcon’s Sitelink3D software.
The pandemic also gave customers time to review their processes and, consequently, realise how digital solutions could improve their current offering and workflows to boost productivity and profits. As restrictions lifted, the demand for – and scarcity of - skilled workers to tackle the project backlog meant that managers needed digital solutions to speed up projects and ensure maximum accuracy and output.
With skilled workers being hard to find, contractors are realising that even simple tasks – putting pegs into building foundations, for example - can be a challenge. Instead of paying out for expensive engineers to do these tasks, they are buying machine control solutions as a long-term, reliable investment.
What support is available?
Since April 2021, increased tax breaks have been available for companies investing in new equipment until April 2023, and cloud computing also became eligible for tax relief3. For every £100 spent, companies can receive tax credit of £130, which will help businesses that are hesitant to invest in digital solutions to make the switch.
The Chancellor’s most recent Autumn Budget gave more hope and optimism to the built environment sector. There will be significantly greater funding available for both adopting digital and upskilling teams which, in addition to tax relief, will help contractors to start using digital solutions if they cannot afford the initial investments.
Firstly, the Chancellor has confirmed £65 million for digitalising England’s planning system. This will help contractors make the move to digital to streamline the planning stage with a fully digital project workflow.
Post-16 education is also set to receive huge investment, with new T-levels in survey, planning and onsite construction. The Chancellor also announced £170million for apprenticeships and training which will help contractors welcome both new skilled workers and upskill existing employees.
Manufacturers such as Topcon are supporting contractors with upskilling by offering the support team’s expertise both before and after purchases to ensure customers are choosing the right kit for them and are able to make the most of their investments. Through training solutions like myTopcon, users can receive extensive online training as well as firmware and software updates to ensure they can use new and existing kit with ease.
The future of digital
As manufacturers and the government encourage contractors to adopt and embrace digital to transform workflows, we must remember that replacing skilled construction workers with technology is not the solution – the two must support each other to be effective. Companies must make the most of the training and ongoing support on offer in order to tackle and overcome the industry’s skill shortage.
1. https://www.citb.co.uk/media/v...
2. https://www.podbean.com/ew/pb-...
3. https://www.theconstructionind...
Andy Flood is UK Business Manager for Topcon Positioning GB (https://www.topconpositioning.com/gb/)